Case Study
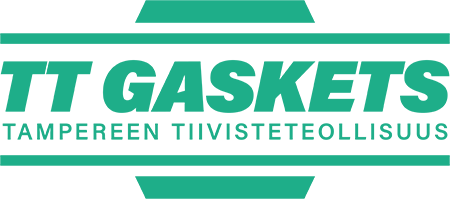
Company Profile
Company: TT Gaskets
Size: €17M
Location: Finland
Machine: Planar P70.20
TT Gaskets is the leading Nordic manufacturer of gaskets, packings and sealing solutions for all major industries including automotive, marine, food processing, lighting and HVAC. The company is an independent, Finnish family business, established in 1943 when Finland needed innovative ammunition -boot grease- and sealing solutions for the needs of the Finnish defense forces.
Today, most of the company’s products and services are exported, mainly to the Nordic countries and Central Europe but also to Asia and North and South America. Manufacturing remains in Finland, at the company’s hometown Tampere.
TT Gaskets were using calipers and other manual measuring devices to inspect their parts. They found that not only was the method slow, but they couldn’t measure all the dimensions of many parts. For example, distance between two holes was not possible to measure with calipers. They also couldn’t verify many GPS tolerances.
“The main benefit is that our whole quality system relies on the machine, and >90% of the time we have a more accurate measuring method than our customers do. Also, the reverse engineering feature saves us a LOT of time, tens of minutes per complex part.”
— Markus Riuttaskorpi, Quality Engineer, TT Gaskets
Figure 1: Planar 2D (P70.20) installed in TT Gaskets, Finland.
They saw the InspecVision Planar machine at Euroblech, the international sheet metal working technology exhibition which takes place in Hanover, Germany, and decided to invest.
Markus Riuttaskorpi, Quality Engineer at TT Gaskets explained that “the amount of time the Planar machine typically saves is 1-2 minutes per part, but that’s not the main bene t of the machine.The main bene t is that our whole quality system relies on the machine, and >90% of the time we have a more accurate measuring method than our customers do. Also, the reverse engineering feature saves us a LOT of time, tens of minutes per complex part.”
Depending on how complex the parts were,TT Gaskets would have spent 4-5 mins per part on inspection.With approximately 50 different parts per week to inspect, the process was taking 4 hours to complete. Markus had no difficulty justifying the investment in the Planar machine with a payback period of only 1-2 years. He says the machine is easy for the quality engineers and packing operators to use and has allowed more work to be assigned to the factory.
He says he would have no hesitation in recommending the Planar machine to another company as “the price-quality ratio is very good on Planar machines. The technical support is also fast, very committed, helpful and professional”. As the machine has no moving parts it is easy to support.
Figure 2: Typical part being measured on the Planar at TT Gaskets.
“Planar machine is a very exciting, versatile and exible tool to have in a factory that manufactures flat parts. It is very fast, and it measures the parts very thoroughly. The amount of measuring points in a small part can be over 10,000, which would take forever to measure for example with CNC coordinate machine. Also it is pretty much the only machine/tool that can measure very soft parts that will deform on a very slight touch.”
— Markus Riuttaskorpi, Quality Engineer, TT Gaskets
To find out more information about the Planar and how it can help your business; please download our online brochure and contact our sales team at sales@inspecvision.com.