Case Study
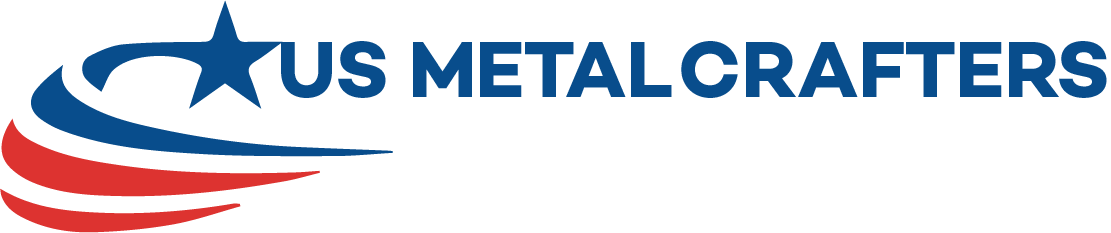
Company Profile
Company: US Metal Crafters
Size: $6.5M
Location: North Carolina,USA
Machine: Planar P150.35 with OS1000.35
US Metal Crafters was formed in 2018 when local business developer Steve McDaniel acquired the assets of the former Speed Metal of Archdale, NC., returning the company from Chinese to US ownership. This could not have come at a better time as many companies look to reshore and streamline their supply chain.
With new US based leadership and a strategy to become the metal fabricating service provider for the largest manufacturing OEMs in the area, the company has already invested over $1.5 million in facility, equipment and software and now offers a complete metal crafting solution of laser cutting, metal stamping, roll forming, fabrication, assembly, and tool and die design in its ISO 9001:2015 certified facility.
“We have been very pleased with our experience with both the machine and customer service at InspecVision. It has been a talking point of shop tours and customers have been very impressed.”
— Meredith Barnes, Marketing Manager, US Metal Crafters
Figure 1: US Metal Crafters Factory, North Carolina
Meredith Barnes, Marketing Manager at US Metal Crafters, explained that there was a need to increase speed and accuracy to maximise their product ow. They were using manual tools such as calipers, protractors and tape measures to inspect parts. Larger and more complex parts were both difficult and very time consuming to check so they began researching ow improvement and QA tools online and found InspecVision’s North American distributor, Productivity Quality Inc.
A decision was made to invest in a 2D and 3D combined system which is used in production four to five times a day. “We inspect an average of 20 parts per week on the InspecVision machine. It was taking approximately 20- 45 minutes to inspect each part manually but this has been reduced to 5-10 minutes per part with the Planar system.” said Meredith.
Figure 2: Operator reviewing a report on a part.
According to Meredith, it wasn’t difficult to justify the investment when they took into account the speed, accuracy and credibility it gave them. “It has been a great sales closing tool for new customers!”
The QA Manager, engineers and associates are the regular users of the machine and they have found both the machine and the software very easy to use. Meredith confirmed they are able to check a higher percentage of parts as they are being produced and said “we are able to complete our QA process more efficiently allowing more room for additional work. It has also given us more credibility with customers and proves our commitment to QA. We would absolutely recommend the InspecVision machine for increasing both accuracy and efficiency.”
“We would absolutely recommend the InspecVision machine for increasing both accuracy and e ciency.”
— Meredith Barnes, Marketing Manager, US Metal Crafters
Figure 5: Part being measured at US Metal Crafters.
When asked about support and maintenance, Meredith replied “Support has been great! We have only required support once as there are no moving parts in the machine so nothing to break down. The machine has no issues on the factory floor and never requires maintenance -just an occasional cleaning or calibration.”
She sees the main benefits as both the ability to check production parts from laser very quickly and more frequently and the ability to quickly create first article inspection reports and begin production runs.
Figure 6: Customer visit at US Metal Crafters.
To find out more information about the Planar and how it can help your business; please download our online brochure and contact our sales team at sales@inspecvision.com.